Member for
5 years 3 monthsCompany Logo
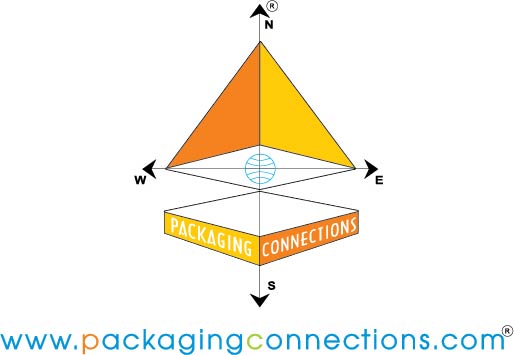
Company Name
Sanex Packaging Connections Pvt Ltd
Designation
Technical Advisor Ebusiness Technology
Email
ch.bhaskar@packagingconnections.com
Facebook Url
First Name
Bhaskar
Gender
Male
Last Name
Ch
LinkedIn Url
Member type
Phone
9811229751