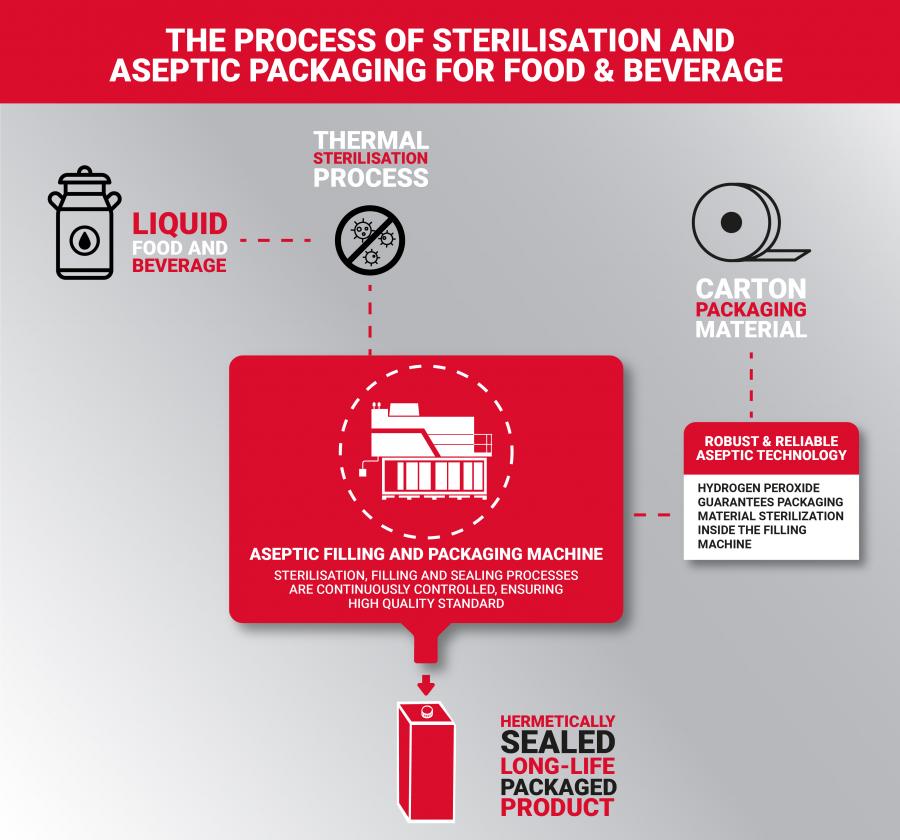
The aseptic packaging market is estimated to grow at a CAGR of 10.89%, from $39.6 billion in 2017 to $66.5 billion by 2022. The growth is mainly driven by the rapid expansion of end-use industries such as food & beverage and pharmaceuticals. Primary factors pushing the field upwards are the rising demand for convenience and quality products, a change in consumer lifestyle, the growth of the dairy beverage market. Progress in developing countries inflates the demand for packaged food & beverages as well as natural products such as flavoured milk and juices.
As of today, the main segment is food and dairy, with a 57% share. Consumption-wise, cartons are the most common packaging material in the aseptic beverage market (51% share) as well as in the entire sector of aseptically-packaged products (72% share).
Aseptic packaging- Principle
Aseptic packaging consists in the process of aseptically packing food & beverage and pharmaceutical products right after sterilisation, executed through UHT (Ultra High Temperature). This is different from the standard process, where sterilisation is performed after packaging rather than before.
In addition to sterilisation, another factor that significantly impacts shelf life is the material in use. The most common one is polylaminate, also known as multilayer aseptic carton. Polylaminate is crucial, as it decreases the exchange of oxygen with the environment while also working as a barrier against light - two elements that, if they both came into contact with the product, might negatively alter it.
History
Aseptic packaging was invented in the late 1920s, but soon discarded due to high costs and inflexibility. The technology, simply, was not mature enough. During the following decades, though, development was tremendous, leading to consumer-size aseptic packages becoming very common in the 1960s across the milk industry in Europe. At that time, Europe did not have the commercial refrigeration capacity to transport milk from rural dairies to the urban centers. The solution came in the form of carton bricks, so named because of the peculiar shape resembling a building brick.
Carton bricks guarantee several advantages over traditional milk packaging methods. For one, they do not need refrigeration, since the aseptic packaging process ensures long shelf life at ambient temperature. Also, their characteristic brick-like shape makes them easy to stack and space saving. These factors among many others determined the popularity of aseptic carton packaging.
In packaging, multilayer aseptic carton refers to thin multilayer structures made by combining layers of paperboard, plastic and aluminium. Multilayer aseptic carton for milk and beverages can be single portion and family size.
Depending on the expected shelf life, it can have two different structures:
- 3-layer polylaminate for short shelf lives, the layers being polyethylene, paperboard, and polyethylene, it is used for pasteurised products
- 7-layer polylaminate for longer shelf lives (i.e. up to 12 months - please note: the effective duration of the shelf life depends entirely on the liquid product). The 7 layers are polytethylene, printing, paperboard, polyethylene, aluminium, adhesive resin, and polytethylene.
The long shelf life is achieved thanks to the additional aluminium layer, today as thin as a few µm, that is inserted between the paperboard and the internal polyethylene layer.
Each layer in the structure has its own importance, like first layer gives protection from moisture and external agents, second layer Makes the packaging recognisable and appealing, third layer ensure the recipient is sturdy and firm, fourth layer helps in adhesion between carton and aluminium film, fifth layer works as light and gas barrier and preserves nutritional value and flavour and aroma at ambient temperature, sixth layer which is adhesive resin layer ensures the adhesion between the two and seventh layer has an alimentary use as it come direct contact of product.
Polyethylene is used for moisture protection, sealing, and as a promoting agent. Each polyethylene layer is made with a different kind of resin:
- The external layer made of Low Density Polyethylene (LDPE) protects the second layer (printing), provides moisture, and ensures functional stability to the flaps of the brick. In this layer an innovative, non-standard practice that a few players, including IPI, employ is to use biopolymers derived from sugarcane, the use of which increases the vegetable and renewable component of the packaging solution.
- The middle layer consists of an adhesive resin that makes the aluminium foil stick to the paperboard.
- The internal layer made of Linear Low Density Polyethylene (LLDPE) provides sealing as well as mechanical properties.
The advantages of multilayer aseptic carton
Multilayer aseptic carton delivers many advantages from a business, consumer, and marketing perspective.
Business-wise:
- It ensures a long shelf life at ambient temperature.
- Contrary to in-container sterilisation, it maintains the food nutritional and sensory properties.
- It is space saving, and therefore more cost-efficient in terms of storage space.
- It is more energy-efficient to produce.
- The package can be formed simultaneously with filling through a single form-fill-seal process. It protects the product from contamination.
Consumer-wise:
- It offers the highest degree of protection.
- It is light, easy to baggage, and safe.
- It is easy to stow and to stack.
- Disposal is a non-issue, since a multilayer aseptic carton is foldable.
- It provides a large area that can be exploited for marketing information and branding.
- Last but not least, it has a distinctive “eco-friendly” feeling.
Marketing-wise:
- It provides a large area for graphics that can be exploited for branding.
- The brick’s shape can be irregular, so as to perfectly fit the brand identity.
- It is eco-sustainable, and sustainability sells.
- The process of sterilisation and aseptic packaging for food & beverage .
Aseptic packaging is accomplished by following these steps:
1. The liquid food product goes through a process of thermal treatment, which leads to a commercially sterile product.
2. The packaging material is sterilised in a dedicated zone inside the packaging machine.
- At the start of every production cycle, the packaging machine itself is sterilised and kept in sterile conditions during the whole production, ensuring that the environment is completely sterile during the entire packaging process. This way, the sterilised product and the sterilised packaging material come together in a sterile environment. The result is a hermetically-sealed long-life packaged product.