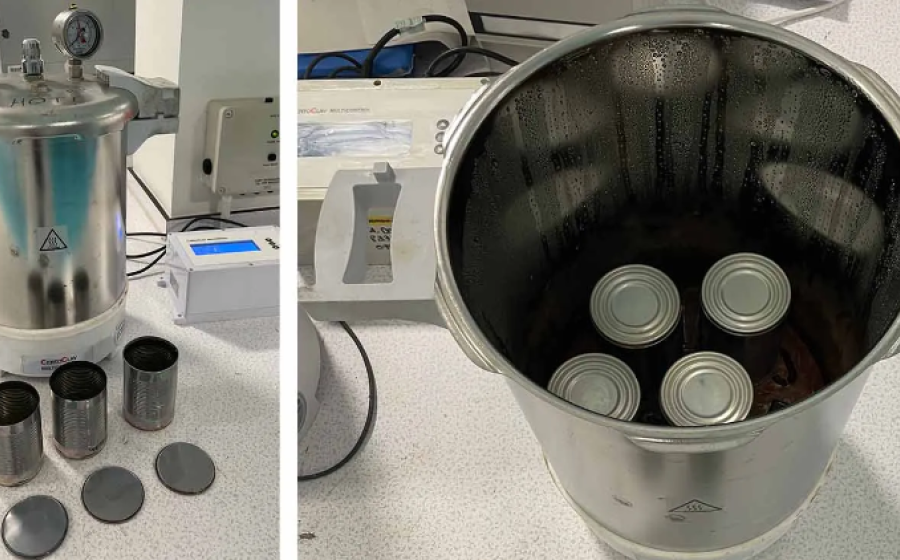
Humble Tin Can Revealed as a High-Tech Marvel by Swansea University Researchers
What may seem like a simple, old-fashioned tin can is, in fact, a product of cutting-edge science and engineering, as researchers at Swansea University’s Steel and Metals Institute (SaMI) have revealed. To mark their 1,000th research collaboration with Tata Steel, SaMI researchers have shared a glimpse into the rigorous testing and innovation that ensure food cans perform safely and effectively.
Far from being a relic of the past, steel is a thoroughly modern material, with over 3,500 grades available—75% of which have been developed in the last 20 years. Its versatility spans industries from construction to renewable energy, and its role in food packaging highlights its surprising sophistication.
The Science Behind the Can
What we call "tin cans" are mostly made from a steel base, often coated with a thin layer of metal like tin and, in some cases, an internal polymer lining. This combination offers unparalleled advantages:
- Preservation: Food cans protect contents from spoilage, retaining nutritional value and flavor.
- Durability: Stronger than plastic and cartons, less fragile than glass.
- Energy Efficiency: No refrigeration required, reducing energy use.
- Sustainability: Steel cans can be endlessly recycled, making them a key player in the push for greener packaging.
But ensuring the safety and reliability of food cans is no small feat. Given that they store food, often for extended periods, these containers must meet exceptionally high performance and quality standards. This is where SaMI’s work with Tata Steel comes in.
Testing the Limits
At SaMI’s advanced facility, researchers replicate real-world conditions to rigorously test the performance of packaging steels. This includes simulating the effects of years of use in just a few weeks. The process involves filling cans with food simulant solutions, sealing them under vacuum, and sterilizing them under high pressure and temperatures.
“We analyze how different steels interact with various foodstuffs, such as acidic or salty substances,” explains Dr. Barrie Goode, Director of Industrial Research and Development at SaMI. “Our accelerated tests fast-forward time, allowing us to ensure the can’s structure and safety hold up over years of potential use.”
Using advanced tools like electron microscopes and energy dispersive spectroscopy, researchers examine cans at microscopic levels for signs of corrosion, lacquer blistering, discoloration, or structural weaknesses. Each test addresses a crucial question: Does the can still meet the strict quality and safety standards demanded by consumers?
A Greener Future
SaMI’s research is not just about today’s cans; it’s shaping the future of steel. Collaborating with Tata Steel, the team is advancing the use of recycled scrap steel, which has far lower carbon emissions than raw materials. They are also investigating hydrogen's effects on steel as part of a broader effort to develop hydrogen transport technologies critical for achieving Net Zero goals.
“Steel is not only essential for packaging but is also a key enabler for a sustainable future,” notes James Edy, Coatings Researcher at Tata Steel. “The rigorous testing we undertake with SaMI gives us confidence in the products we deliver to customers, and by extension, to consumers.”
Modern Marvel
Thanks to this meticulous research and innovation, the humble food can is anything but simple. Behind every can of beans or soup lies a high-tech marvel of material science, ensuring safety, quality, and sustainability. As industries evolve, the work of SaMI and Tata Steel demonstrates how even everyday objects are reimagined for a better future.
So next time you open a can of baked beans, remember: it’s not just a container—it’s a 21st-century wonder.